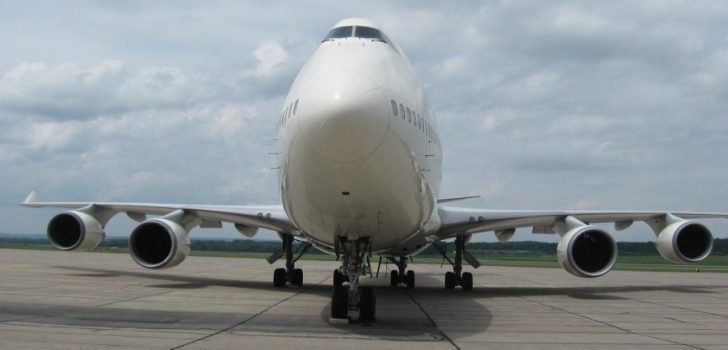
Frequently Asked Questions
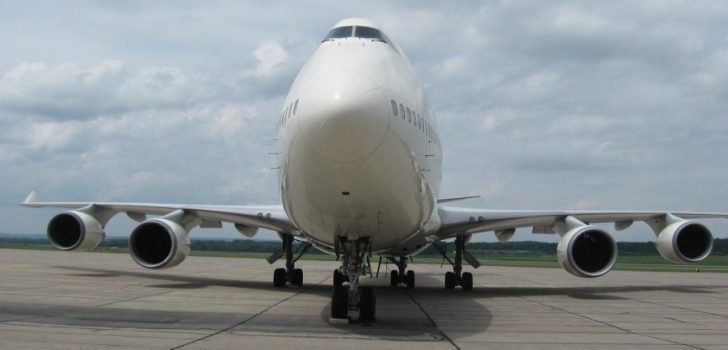
Seat cushions and covers must meet the vertical burn and fire blocking requirements. The vertical burn requirement is met separately for cushions and covers but the fire blocking requirement needs to be met with the cushion and cover together during the certification test. This is why it is important to determine the effect on original fire blocking certification when changing dress covers or cushions.
HOW TO DETERMINE SEAT CUSHION/COVER CERTIFICATION:
REQUIREMENTS
Seat cushions and covers must meet the vertical burn and fire blocking requirements of FAR 25.853 which refers to parts of appendix F for further details. The vertical burn requirement is met separately for cushions and covers but the fire blocking requirement needs to be met with the cushion and cover together during the certification test. This is why it is important to determine the effect on original fire blocking certification when changing dress covers or cushions.
WHEN LOOKING AT CUSHIONS AND COVERS
Find a vendor and part number on the cushion.
Look for a statement that cushion meets FAR 25.853(c) when used with approved dress cover (these words can vary from vendor to vendor but the key is FAR 25.853(c) or (b) if done when fire blocking was under paragraph b).
Try to trace the information on the cushion tag to the part number on the dress cover tag. If so, the certification is valid. If not, obtain the fire blocking certification report from the cushion vendor and find what dress cover is certified with that cushion.
If no tag is present on the cushion or cover, there is no confidence that either assembly has any approval basis.
If there is damage to the cushion fire blocking layer or the dress cover, the flammability characteristics may have be compromised and it should be replaced.
WHEN LOOKING AT FIRE BLOCKING REPORT
Find the P/N of the cushion and cover in the report and compare with that on the parts in question.
If same, the certification is valid. If the cushion but not dress cover can be found, the dress cover material must be tested with the cushion material per appendix F of FAR 25 or certification by similarity may be possible.
If no part numbers can be found in the report, the vendor may have an internal document that traces the raw materials mentioned in the report to the part numbers stamped on the parts (perhaps a drawing number listed in the report).
Any new testing must be done by a lab with the correct calibrated equipment. Sending a sample of the cushion is not adequate because you do not know the materials and the test cushions are of a different size than the production cushions. FAA conformity inspection of test samples is required for obtaining 8130-3 tag.
APPROVING DRESS COVER CHANGE BY SIMILARITY
- The following is required to determine approval by similarity rather than test:
- The original fire blocking test report for the cushions being used.
- The new dress cover raw material identification number and vendor.
- The new dress cover weight, material composition and vertical burn results.
After analysis of the above, a DER can prepare and approve a report if criteria are met.
In 1988, the FAA issued regulations requiring that all newly developed transport aircraft use dynamically tested “16g” seats. Using a anthropomorphic test dummy (ATD), these seats undergo dynamic testing and evaluation regarding injury protection. These requirements are part of the type certificate of the aircraft.
When is it required?
Head Injury Criteria (HIC) is one of many required tests for “16g” seats but it may or may not be applicable to a specific aircraft.
For example, a newly design aircraft type as the Airbus 350 must meet ALL the “16g” requirements including HIC. However, new aircraft models as the Boeing 737-800 or 737-9 that are “16g” aircraft are exempt from HIC requirements unless the aircraft is manufactured after October 27 of 2009 and in a 121 operation (US carrier). This requirement to a later standard is an FAA operational requirement and not a design or type certificated requirement.
What is HIC?
Head Injury Criteria (HIC) is one of many required tests for “16g” seats. HIC is part of a series of test to determine the likelihood of head injury arising from an impact. For seats, the tests measure the impact of the test dummy’s head to back of the seat or the surface (monument) in front.
Example of aspects to consider for a “HIC” aircraft seat installation:
-Seat Pitch:
The seat manufacturer determines an allowed seat pitch depending on the number of tests performed during certification and the results of these tests. Some of the seat characteristics that may affect HIC test results are monitors, tray table designs, tray tables latches, exposed metal parts, etc.
Some seat manufacturers test only for a specific pitch range depending on the customer requirements during the seat certification. There are basically two ways to install these seats outside the manufacture’s seat pitch limitations. One is to perform a series of HIC tests to certify the seat at the desired pitch (in the case that the manufacturer did not test the seat at the desired pitch). The second option is to install the seats at such a large pitch that the passengers head would not hit the back of the seat in front.
-Seat Setback:
The seat manufacturer determines the allowed setback from a monument or other structure by measuring the head path of the dummy during test. The minimum setback to a structure is the distance that the seat manufacturer has determined so the passenger’s head does not impact the structure in front.
These limitations for pitch and setback are usually published in the Seat’s Installation and Limitations Instructions document from the seat manufacturer.
The minimum seat pitch is defined by the aircraft and seat manufacturers but the seat installation is still dependent, but not limited to, the factors listed below:
a) Seat weight. Aircraft manufacturers sometimes limit the seat pitch depending on the seat weights. A group of heavy seats could impose high loads too close together that may affect the integrity of the aircraft structure.
b) Seat interface loads. These are the loads that a single seat impose into the aircraft seat track at the attachment points. A heavy seat with a high CG and short longitudinal leg spacing could have higher interface loads that may exceed the aircraft seat track allowables. The seat track could fail and the seats could come loose.
c) Seat permanent deformations. The seat manufacturer records the seat permanent deformations after a series of static and dynamic tests. The seat installer must make sure that all the passengers have enough room for egress considering the published seat deformations. This is done to prevent passengers getting trapped in between seats and to allow for a speedy evacuation in case of an emergency.
d) Head Injury Criteria. See ” What is a HIC aircraft and when is it needed?”
Factors a, b (above) could be substantiated by further structural analysis of the aircraft seat tracks.
There is a long list of items that related to the number of passengers and/or crew seats in the aircraft. Some of the aspects or systems that should be considered when changing the aircraft’s passenger configuration are:
-
- Emergency Equipment: Some of the emergency equipment quantity like portable oxygen bottles, life rafts and fire extinguishers are dependent of the number of occupants.
- Passenger Service Units (PSU): PSU must be re-distributed and sometimes replaced to comply with the location and mask quantities requirements.
- Escape path lighting system: An escape path lighting evaluation should be performed to determine if it still meet the installers requirements like distance between lights, floor paths location relative to the seats and the ability to recharge light strips (if photoluminescent system), etc.
- Location and quantity of speakers for PA announcements.
- Placard and sign visibility from seated positions.
- Direct view of passenger seats by flight attendants.
- Meeting the required aisle width, passageway and flight attendant assist space.
- Evaluate proximity of seats to potentially injurious objects.